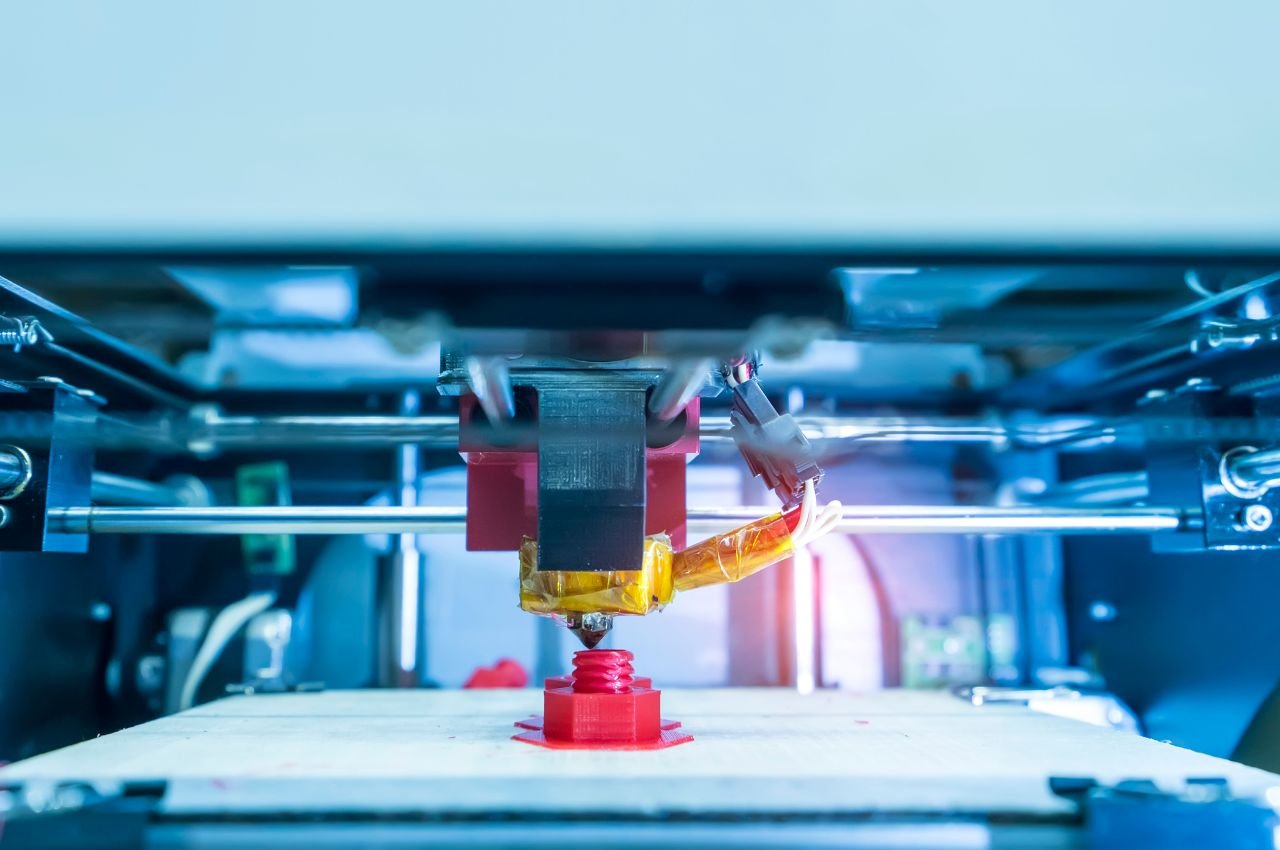
Introducing Polymer 3D Printing: Advanced Solutions in Australia
Ripley Dynamics introduces the world of polymer 3D printing, a realm where advanced solutions meet the diverse needs of industries across Australia. Polymer 3D printing encompasses a variety of techniques, including Fused Deposition Modeling (FDM) and Selective Laser Sintering (SLS), enabling the creation of high-quality, complex designs with a broad range of thermoplastic materials. These materials offer varied properties, from high flexibility to substantial strength, catering to a myriad of applications.
Our services in polymer 3D printing stand out due to their precision, efficiency, and adaptability. The technology is perfect for producing prototypes, end-use parts, and customized components across sectors such as automotive, aerospace, healthcare, and consumer goods. The versatility of polymer materials allows for innovation in design, enabling lighter, stronger, and more efficient products.
At Ripley Dynamics, we continuously invest in cutting-edge technologies and materials to ensure our polymer 3D printing services remain at the forefront of the industry. By partnering with us, Australian businesses can leverage the full potential of polymer 3D printing for their product development, prototypes, and manufacturing needs.
Exploring the Capabilities of PEEK Filament in 3D Printing
Ripley Dynamics is exploring the remarkable capabilities of PEEK (Polyether Ether Ketone) filament in 3D printing, offering Australian industries a material with exceptional properties. PEEK is renowned for its high temperature resistance, mechanical strength, and chemical stability, making it an ideal choice for demanding engineering applications.
The use of PEEK in 3D printing opens up possibilities for creating parts that can withstand harsh environments, including high temperatures and corrosive chemicals. This makes it highly suitable for specialized applications in aerospace, automotive, and medical industries. For instance, PEEK is used in the medical field for creating implants and surgical instruments due to its biocompatibility and sterilization resistance.
At Ripley Dynamics, our expertise in 3D printing with PEEK filament ensures that we can produce parts that meet the highest standards of quality and performance. Our clients can take advantage of PEEK’s exceptional properties to innovate and excel in their respective fields, pushing the boundaries of what's possible in high-performance applications.
Advancements in Thermoplastic 3D Printing: Pushing the Boundaries
Ripley Dynamics is at the forefront of advancements in thermoplastic 3D printing, pushing the boundaries of what's possible in additive manufacturing. With a focus on innovative materials and state-of-the-art printing technologies, we are redefining the limits of design and functionality in 3D printed parts.
Thermoplastics, due to their excellent mechanical properties and ease of processing, are a popular choice for 3D printing. They offer versatility in applications, ranging from rapid prototyping to production of functional end-use parts. Advancements in this area have led to the development of thermoplastics with enhanced properties, such as increased strength, improved heat resistance, and better durability, making them comparable to traditional manufacturing materials.
Our commitment at Ripley Dynamics is to stay updated with these technological advancements, incorporating new materials and methods to offer our clients innovative solutions. This approach allows us to tackle complex challenges and meet the high standards expected in industries like automotive, aerospace, and healthcare.
High-Performance Polymer Filaments: The Backbone of Quality 3D Printing
High-performance polymer filaments are the backbone of quality 3D printing services offered by Ripley Dynamics. These materials, known for their superior strength, durability, and thermal stability, are pivotal in producing parts that can withstand demanding applications. We specialize in a range of high-performance polymers, including PEEK, PEKK, and Nylon, each chosen for its unique attributes to suit specific project requirements.
Our selection of polymer filaments ensures that we can provide solutions for a wide range of industries requiring parts with specific performance criteria. Whether it’s components that need to endure high temperatures in aerospace, medical devices requiring biocompatibility, or automotive parts that demand high strength and durability, our high-performance polymers are up to the task.
At Ripley Dynamics, we understand the importance of using the right materials to achieve optimal results in 3D printing. Our expertise in selecting and printing with high-performance polymers allows us to deliver products that meet the highest standards of quality, functionality, and reliability.
PEEK 3D Printing Applications: Versatility Meets Innovation
PEEK 3D printing applications are a testament to where versatility meets innovation, a domain expertly navigated by Ripley Dynamics. Polyether Ether Ketone (PEEK) is a high-performance thermoplastic known for its exceptional mechanical, thermal, and chemical resistant properties, making it ideal for a variety of challenging applications.
In the aerospace industry, PEEK is used for components that require lightweight yet strong materials capable of withstanding high temperatures and pressures. In the medical field, its biocompatibility makes it perfect for surgical implants and medical devices. The automotive industry utilizes PEEK for creating durable, heat-resistant parts that contribute to vehicle efficiency and safety.
The versatility of PEEK extends to the electronics industry for creating insulative and heat-resistant components and to the oil and gas sector for parts that must endure harsh chemical and temperature environments. Ripley Dynamics’ expertise in PEEK 3D printing allows industries to harness this material's full potential, leading to innovative solutions and advancements in product development and manufacturing.
Introducing Polymer 3D Printing: Advanced Solutions in Australia
Ripley Dynamics introduces the world of polymer 3D printing, a realm where advanced solutions meet the diverse needs of industries across Australia. Polymer 3D printing encompasses a variety of techniques, including Fused Deposition Modeling (FDM) and Selective Laser Sintering (SLS), enabling the creation of high-quality, complex designs with a broad range of thermoplastic materials. These materials offer varied properties, from high flexibility to substantial strength, catering to a myriad of applications.
Our services in polymer 3D printing stand out due to their precision, efficiency, and adaptability. The technology is perfect for producing prototypes, end-use parts, and customized components across sectors such as automotive, aerospace, healthcare, and consumer goods. The versatility of polymer materials allows for innovation in design, enabling lighter, stronger, and more efficient products.
At Ripley Dynamics, we continuously invest in cutting-edge technologies and materials to ensure our polymer 3D printing services remain at the forefront of the industry. By partnering with us, Australian businesses can leverage the full potential of polymer 3D printing for their product development, prototypes, and manufacturing needs.
Exploring the Capabilities of PEEK Filament in 3D Printing
Ripley Dynamics is exploring the remarkable capabilities of PEEK (Polyether Ether Ketone) filament in 3D printing, offering Australian industries a material with exceptional properties. PEEK is renowned for its high temperature resistance, mechanical strength, and chemical stability, making it an ideal choice for demanding engineering applications.
The use of PEEK in 3D printing opens up possibilities for creating parts that can withstand harsh environments, including high temperatures and corrosive chemicals. This makes it highly suitable for specialized applications in aerospace, automotive, and medical industries. For instance, PEEK is used in the medical field for creating implants and surgical instruments due to its biocompatibility and sterilization resistance.
At Ripley Dynamics, our expertise in 3D printing with PEEK filament ensures that we can produce parts that meet the highest standards of quality and performance. Our clients can take advantage of PEEK’s exceptional properties to innovate and excel in their respective fields, pushing the boundaries of what's possible in high-performance applications.
Advancements in Thermoplastic 3D Printing: Pushing the Boundaries
Ripley Dynamics is at the forefront of advancements in thermoplastic 3D printing, pushing the boundaries of what's possible in additive manufacturing. With a focus on innovative materials and state-of-the-art printing technologies, we are redefining the limits of design and functionality in 3D printed parts.
Thermoplastics, due to their excellent mechanical properties and ease of processing, are a popular choice for 3D printing. They offer versatility in applications, ranging from rapid prototyping to production of functional end-use parts. Advancements in this area have led to the development of thermoplastics with enhanced properties, such as increased strength, improved heat resistance, and better durability, making them comparable to traditional manufacturing materials.
Our commitment at Ripley Dynamics is to stay updated with these technological advancements, incorporating new materials and methods to offer our clients innovative solutions. This approach allows us to tackle complex challenges and meet the high standards expected in industries like automotive, aerospace, and healthcare.
High-Performance Polymer Filaments: The Backbone of Quality 3D Printing
High-performance polymer filaments are the backbone of quality 3D printing services offered by Ripley Dynamics. These materials, known for their superior strength, durability, and thermal stability, are pivotal in producing parts that can withstand demanding applications. We specialize in a range of high-performance polymers, including PEEK, PEKK, and Nylon, each chosen for its unique attributes to suit specific project requirements.
Our selection of polymer filaments ensures that we can provide solutions for a wide range of industries requiring parts with specific performance criteria. Whether it’s components that need to endure high temperatures in aerospace, medical devices requiring biocompatibility, or automotive parts that demand high strength and durability, our high-performance polymers are up to the task.
At Ripley Dynamics, we understand the importance of using the right materials to achieve optimal results in 3D printing. Our expertise in selecting and printing with high-performance polymers allows us to deliver products that meet the highest standards of quality, functionality, and reliability.
PEEK 3D Printing Applications: Versatility Meets Innovation
PEEK 3D printing applications are a testament to where versatility meets innovation, a domain expertly navigated by Ripley Dynamics. Polyether Ether Ketone (PEEK) is a high-performance thermoplastic known for its exceptional mechanical, thermal, and chemical resistant properties, making it ideal for a variety of challenging applications.
In the aerospace industry, PEEK is used for components that require lightweight yet strong materials capable of withstanding high temperatures and pressures. In the medical field, its biocompatibility makes it perfect for surgical implants and medical devices. The automotive industry utilizes PEEK for creating durable, heat-resistant parts that contribute to vehicle efficiency and safety.
The versatility of PEEK extends to the electronics industry for creating insulative and heat-resistant components and to the oil and gas sector for parts that must endure harsh chemical and temperature environments. Ripley Dynamics’ expertise in PEEK 3D printing allows industries to harness this material's full potential, leading to innovative solutions and advancements in product development and manufacturing.